The natural choice
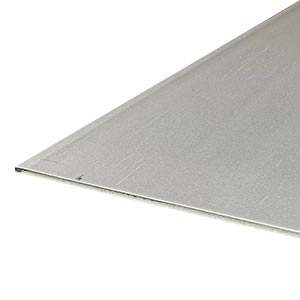
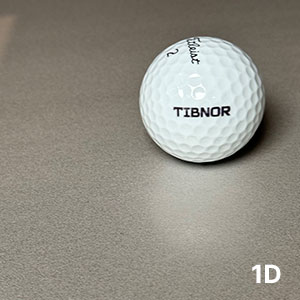
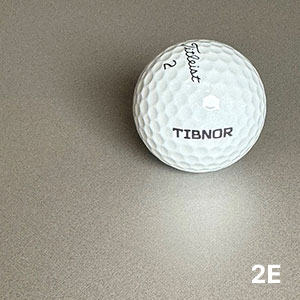
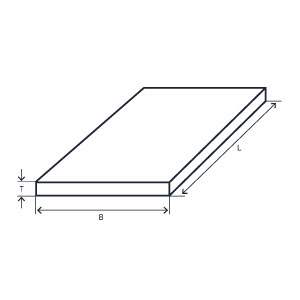
Produktinformation
Tibnor stocks hot- and cold-finished stainless sheet in grade EN 1.4462 which is a so-called duplex stainless steel and as such is characterised by a roughly 50-50 mixture of austenite and ferrite. The content of chromium is higher and that of nickel is lower than for traditional austenitic stainless types such as
EN 1.4404, 1.4432 or 1.4436 but in common with these grades 1.4462 is alloyed with molybdenum. The steel is also alloyed with nitrogen. The yield strength of 1.4462 is about double that of the austenitic steels mentioned.
Flat formats of 1.4462 are standardised in EN 10088-2. This standard covers hot-finished sheet with thicknesses up to and including 13.5 mm and cold-finished sheet up to and including 8 mm.
Thanks to the high content of chromium in combination with molybdenum and nitrogen, 1.4462 is characterised by excellent corrosion resistance even in aggressive environments, especially those with high chloride content (sea water). Furthermore, its duplex character renders the steel much more resistant than austenitic types to stress-corrosion cracking in chloride-laden environments. Its good corrosion resistance along with high strength makes the material an attractive alternative for load-bearing constructions, with chemical plant and the marine and offshore segments meriting special mention.
1.4462 is relatively easy to weld using the same procedures as for austenitic steels. Its cold formability is good but the higher strength means that the forces needed will be higher and springback more pronounced than for an austenitic grade with the same dimension.
The cold-finished sheet that is stocked has surface finish 2E (annealed with scale removed mechanically) whereas the finish of hot-rolled sheet is 1D (annealed and pickled).
Tibnor stocks hot- and cold-finished stainless sheet and plate in the austenitic heat-resistant grade EN 1.4835. Austenitic steels in general have good high-temperature properties but 1.4835 is alloyed with, apart from chromium and nickel, silicon and cerium which confer even better creep strength and oxidation (scaling) resistance. The material can handle continuous or cyclic exposure up to 1150°C. The high content of chromium along with the additions of cerium and silicon ensure that the oxide layer remains intact and does not spall even under cyclical temperature conditions. The steel also contains small but controlled amounts of nitrogen and carbon which impart a somewhat higher room-temperature strength than for 1.4301 or 1.4404.
Flat formats of 1.4835 are standardised in EN 10095 which covers cold-and hot-finished sheet and plate up to thickness 75 mm.
1.4835 is optimised for use at high-temperatures but the resistance to aqueous corrosion at normal temperatures is still reasonable, somewhat better than 1.4301 and 1.4307. Based upon its favourable high-temperature properties, 1.4835 is used extensively in furnaces and kilns as well as exhaust systems and in plants for production of chemicals and energy.
Being austenitic, 1.4835 is easy to weld. With a correct procedure and suitable consumables, welds will exhibit the same favourable high-temperature properties as the base steel. Its cold formability is good but the somewhat higher base strength means that the forces needed will be higher than for the same dimension in an austenitic grade like 1.4301 or 1.4404.
The cold-finished sheet that is stocked has surface finish 2E (annealed with scale removed mechanically) whereas the finish of hot-rolled sheet and plate is 1D (annealed and pickled).